Are you exploring the world of large-scale machining and encountering terms like “gantry mill“? A gantry mill is a type of Computer Numerical Control (CNC) milling machine characterized by its bridge-like structure, which allows for machining very large and heavy workpieces with high precision. This article will provide a comprehensive understanding of gantry mills, detailing their operation, advantages, common applications, and how they differentiate from other CNC machinery.
Table of Contents
ToggleWhat is a Gantry Mill?
A gantry mill is a large-scale, high-precision Computer Numerical Control (CNC) machine tool designed for machining oversized workpieces, defined by its distinctive gantry structure where the cutting head or spindle moves along a horizontal bridge supported by two vertical columns, spanning over the stationary or moving workpiece. This configuration allows for exceptional stability and accuracy when processing large components.

Unlike conventional milling machines where the spindle is affixed to a column and the table moves, gantry mills typically feature a stationary or minimally moving table. The gantry, carrying the spindle, traverses along the length of the machine bed. This design makes gantry mills ideal for heavy-duty cutting operations on large parts that are difficult or impossible to move on smaller machines. They are crucial in industries requiring precision on a massive scale.
How Does a Gantry Mill Work?
A gantry mill operates by moving a cutting tool, mounted on a spindle, along multiple axes within a bridge-like frame that spans over the workpiece, which typically remains stationary on the machine bed. The gantry structure, controlled by CNC programming, moves the cutting tool precisely over its surface, allowing for the efficient removal of material from large, heavy components.
The gantry consists of two parallel side supports (columns) connected by a horizontal beam (bridge), on which the spindle carriage travels. The workpiece is secured on a large table beneath the gantry. The CNC system directs the movement of the gantry along the X-axis (longitudinal), the spindle carriage along the Y-axis (transverse on the bridge), and the spindle’s vertical movement along the Z-axis. Some advanced gantry mills also include rotational axes for complex 3D machining. This coordinated movement ensures high accuracy and repeatability across the entire large working envelope.
What are the Primary Advantages of Gantry Milling?
The primary advantages of gantry milling include their unparalleled ability to machine very large and heavy workpieces, superior rigidity leading to high precision, and efficient material removal rates. Their robust structure minimizes vibration and deflection, ensuring excellent surface finishes and dimensional accuracy even on demanding applications, making them indispensable for industries handling massive components.
Here are key benefits of using gantry mills:
- Large Workpiece Capacity: Gantry mills are specifically designed to accommodate components too large for standard milling machines, such as aerospace frames, ship propellers, and large mold bases.
- High Rigidity and Stability: The bridge-like structure provides exceptional support to the cutting head, significantly reducing vibration and deflection during heavy cutting, leading to superior surface finish and accuracy.
- Precision Machining: Their robust construction and advanced control systems enable tight tolerances and precise machining across large surfaces.
- Heavy Material Removal: Gantry mills are capable of aggressive material removal, making them efficient for roughing large parts and achieving desired dimensions quickly.
- Versatility for Complex Geometries: With multi-axis capabilities (up to 5-axis), gantry mills can create intricate shapes and contours on large components, expanding their application range.
Where are Gantry Mills Commonly Used?
Gantry mills are commonly used in industries that require the precision machining of very large, heavy, and often complex components, such as aerospace, automotive (especially for molds and dies), heavy machinery manufacturing, and energy sectors. Their capacity to handle oversized workpieces makes them essential for these specialized applications.
Specific applications include:
- Aerospace Industry: Machining large aircraft components like wing spars, fuselage sections, and structural frames from tough materials.
- Automotive Industry: Producing large molds and dies for vehicle body panels, engine blocks, and other substantial parts.
- Heavy Machinery Manufacturing: Creating components for construction equipment, mining machinery, and agricultural vehicles.
- Energy Sector: Fabricating parts for wind turbines, power generation equipment, and nuclear components.
- Shipbuilding: Machining propellers, engine blocks, and large structural elements for marine vessels.
- Tool and Die Making: Manufacturing oversized dies for stamping and forming operations.
How Do Gantry Mills Compare to Other CNC Machines?
Gantry mills primarily differ from other CNC machines like vertical machining centers (VMCs) and horizontal machining centers (HMCs) in their ability to handle exceptionally large workpieces and their unique bridge-like structural design. While VMCs and HMCs are versatile for a wide range of part sizes, gantry mills excel in machining dimensions and weights that are impractical for their counterparts.
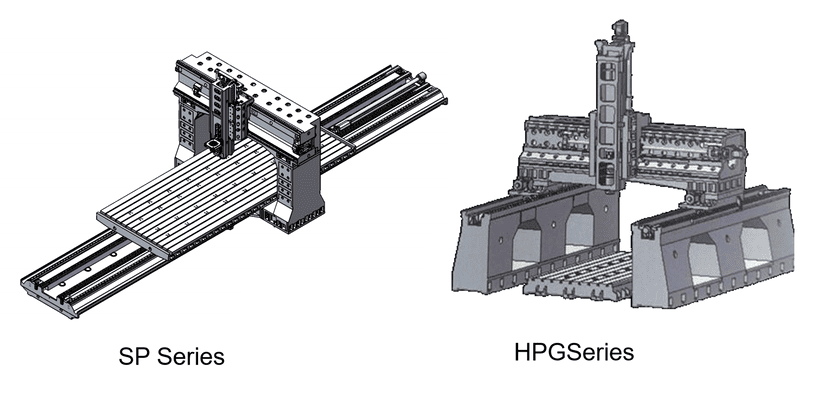
Here’s a comparison:
Feature | Gantry Mill | Vertical Machining Center (VMC) | Horizontal Machining Center (HMC) |
Workpiece Size | Very Large, Heavy | Small to Medium | Small to Medium, often long |
Structure | Bridge-like gantry spanning over workpiece | Vertical spindle, fixed column, moving table | Horizontal spindle, fixed column, often pallet changer |
Workpiece Mvmt. | Typically stationary or limited movement | Table moves in X, Y, Z axes | Table rotates (B-axis), moves in X, Y, Z axes |
Rigidity | Extremely High (due to gantry support) | Good (depends on machine size/design) | Very Good (especially for heavy cuts) |
Best For | Large molds, aerospace parts, heavy structures | General purpose milling, small-medium parts | High-volume production, multi-sided machining |
Footprint | Very Large | Medium | Medium to Large |
What Factors Should You Consider When Choosing a Gantry Mill?
When choosing a gantry mill, critical factors include the maximum workpiece dimensions and weight it can accommodate, the required machining accuracy and surface finish, and the number of axes needed for part complexity. Other considerations are the spindle power and torque for material removal, the machine’s overall rigidity, and the level of automation and control features for efficient operation.
Consider the following points:
- Workpiece Specifications:
- Size (X, Y, Z travel): Ensure the machining envelope is sufficient for your largest planned components.
- Weight Capacity: Verify the table and machine structure can support the heaviest workpieces.
- Machining Requirements:
- Accuracy and Precision: Evaluate the machine’s repeatability and positional accuracy to meet your tolerance demands.
- Surface Finish: Assess the machine’s capability to achieve the required surface quality.
- Spindle Specifications:
- Power and Torque: Match these to the materials you’ll be cutting and the desired material removal rates.
- Spindle Speed: Consider the range necessary for different tooling and materials.
- Number of Axes:
- 3-axis: Suitable for basic planar machining on large parts.
- 5-axis: Essential for complex, multi-sided, and contoured geometries, reducing setup time.
- Machine Rigidity and Construction: Look for robust cast iron or fabricated steel construction that minimizes vibration for stable machining.
- Control System and Software: Ensure the CNC control is user-friendly, powerful, and compatible with your CAD/CAM software.
- Automation and Features: Consider automatic tool changers, chip conveyors, coolant systems, and other features that enhance productivity and ease of use.
- Footprint and Facility Requirements: Gantry mills are large; ensure you have adequate space, foundation, and power supply.
- Budget and Return on Investment (ROI): Evaluate the initial cost against the potential for increased production efficiency and quality.
Conclusion
In summary, a gantry mill is a specialized and powerful CNC machine tool distinguished by its overhead bridge structure, designed specifically for the high-precision machining of exceptionally large and heavy workpieces. Its robust design ensures superior rigidity and accuracy, making it an indispensable asset in industries such as aerospace, automotive, and heavy machinery manufacturing. When selecting a gantry mill, critical considerations include workpiece size and weight, required machining accuracy, spindle power, and the number of axes needed to meet specific production demands. Investing in a gantry mill empowers manufacturers to tackle projects of immense scale and complexity with unparalleled precision and efficiency.
At HIRUNG, we specialize in providing high-quality CNC machine tools designed to meet the rigorous demands of modern manufacturing. Our product line includes advanced CNC Gantry Machines, like the Column Moving Type CNC Big Gantry HPG Series and Table Moving Type CNC Big Gantry SP Series, alongside CNC Vertical Machining Centers and Lathe Machines. With rich experience in CNC machine tool manufacturing, we are committed to delivering affordable solutions built with high-quality components and precision assembly. Our dedication to strict accuracy testing standards and comprehensive after-sales service ensures that our customers receive reliable, high-performance machinery tailored for optimal production.